
A significant enhancement to both the new Standards for the Operation of Licensed Pharmacies (SOLP) and the Standards of Practice for Pharmacists and Pharmacy Technicians is how a pharmacy’s unregulated employees are supervised. Rather than focusing on the concepts of direct supervision and indirect supervision, the new standards require pharmacy teams to examine their policies and procedures and identify the “critical steps” of any processes that require an independent double check by a regulated member.
Within the SOLP, a critical step is defined as “a step in a process that must be reviewed during the process as it cannot be confirmed during a final check. These steps vary by task but may include performing calculations, verifying the selection of drugs or ingredients, verifying quantities of ingredients, or verifying technique.”
In the new standards, an unregulated employee may complete certain steps of an activity to support patient care. However, each identified critical step requires an independent double check by a regulated member before the activity can proceed to the next step. An unregulated employee cannot take these activities from start to finish without these double checks taking place at each critical step.
As defined in the standards, “An independent double check means a regulated member double checks the critical steps completed by another individual at the practice site. In the case of an unregulated employee, a double check is mandatory at each critical step.”
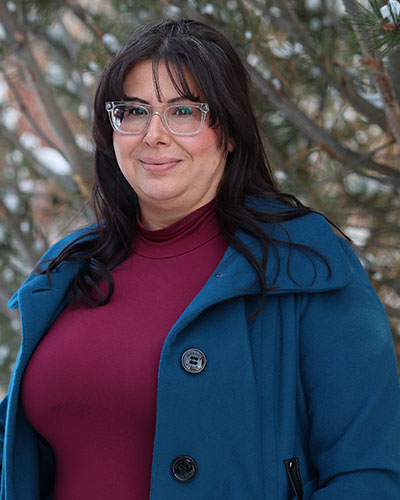
While the new SOLP take effect February 1, 2025, the practice of regulated members performing independent double checks at each critical step already occurs in pharmacy departments within Alberta Health Services (AHS) Pharmacy Services. Pharmacy technician Laura Miskimins is the technical practice manager at AHS and is responsible for managing a team of technical practice leaders who optimize technical practice throughout AHS pharmacy services.
“Unregulated staff, we know them as pharmacy assistants, make up about a quarter of all the pharmacy staff within AHS Pharmacy Services,” said Laura. “Our assistants’ duties typically include things like packaging medications, selecting medications for refills, ensuring ward stock is replenished, and delivering medications within our facilities. The work they do supports regulated members in providing patients the medications they need, right when they need them.”
One example of how AHS has incorporated critical steps and independent double checks is when unregulated employees use an automated repackager to prepare drugs for patients. In this process, pharmacy assistants complete a number of tasks, but there are points throughout that process where a check must be completed by a regulated member—specifically a pharmacy technician or pharmacist who’s been trained on the repackaging machine.
“The pharmacy assistant’s duties might include refilling canisters or filling the special-tablet system or detachable tablet adapter trays, and processing a repackaged batch,” said Laura. “With these duties, we do have checkpoints in place. A pharmacy technician or pharmacist must complete a check of any refilled canisters or trays before they’re placed in the repackaging machine. If a pharmacy assistant encounters an error, an out-of-service message, or an issue when they’re processing a batch, they need to alert a pharmacy technician to support any troubleshooting.”
Pharmacy assistants also prepare a completed repackaging batch for verification by an automated checking machine by collecting the completed spool or reel, and feeding it into the automated checking machine. This is another critical step that requires an independent double check by a regulated member.
“A pharmacy technician is responsible for validating the batch that’s being checked by the machine and for determining whether any error messages are the result of a true error or a false positive,” said Laura. “The pharmacy assistant might assist the pharmacy technician by completing integrity checks to make sure there’s no broken packages or duplicate medications in any of the pouches. However, a pharmacy technician or pharmacist is ultimately responsible for verifying any corrections that have been made and for all final checks prior to dispensing any of the repackaged medication.”
Laura says a lot of thought and consideration of scopes of practice, roles, and supervision requirements went into determining the critical steps in each process that would require an independent double check by a regulated member.
“We considered each activity and some of the questions we asked ourselves were, ‘Who can do this? Who should do this and under what conditions or circumstances? Who is accountable? How do we know that they’re accountable?’ That helped really guide where we put those critical steps in,” said Laura. “I’m sure this work is going to continue to evolve as the new standards come into effect, and we continue to learn and understand more about how to apply them. These questions have helped us identify where we needed to continue to have or introduce new fence posts and critical steps to ensure that our unregulated staff can complete their duties accurately and safely, and our regulated members can meet their professional responsibilities in a timely and efficient manner.”
Many community pharmacies also use automated repackaging machines, and similar critical steps and double checks should be added to their practice.
A similar example of a critical step in community practice would be the drug identification number (DIN) check of a stock bottle when preparing a prescription. While the pharmacy assistant should always check the DIN themselves, this critical step requires an independent double check by a regulated member before the stock bottle is returned to the shelf since positive identification of the drug cannot easily be assured at the end of the process if the drug has been put away.
Using automatic repackaging machines is just one example of a process that pharmacy teams use that would require identification of critical steps and use of independent double checks. As required in the standards, pharmacy teams must review their processes and identify the critical steps in each process that would require an independent double check by a regulated member.
A big reason critical steps and independent double checks are so important in any pharmacy process, says Laura, is that accountability is at the root of everything pharmacy professionals do.
“As regulated members, we’re accountable for the medications that are leaving our pharmacies,” she said. “It means asking yourself, ‘How do I know that what is going out is the right medication for the right patient at the right time, and that all of the appropriate steps were followed?’ I think that comes down to documenting your processes, making sure your staff are aware of them, knowing where those check points are, and the rationale behind why you have them there. It makes everything clearer for everyone, and you’re not worried about someone maybe making an incorrect assumption.”
Ultimately, these requirements are in place to ensure patient safety—a priority for any pharmacy team.
“Having critical steps and independent double checks in place gives everyone more confidence when medications are going out to patients,” said Laura. “It also helps us ensure that we haven’t missed anything. Medications are labelled appropriately, they’re stored appropriately, they’re packaged appropriately, they’ve been handled correctly, and we’ve got the right medication in the right spot. What keeps our patients safe are those checks and having standardized processes. Patients don’t know what’s going on behind the scenes in a pharmacy. It’s our responsibility to make sure that everything that’s going on back there is appropriate and safe. We’re privileged to have the trust patients put in us, and it’s important that we take the appropriate steps to maintain that trust.”