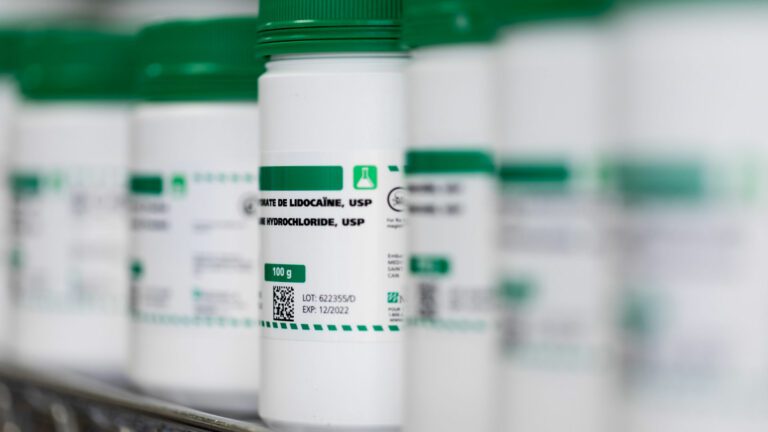
It’s an important challenge when preparing compounds in a non-sterile environment: ensuring the quality of the medications being compounded.
When non-sterile compounding occurs, the products being prepared can be more susceptible to contamination than those prepared in sterile environments. That’s why it is critical that pharmacy teams take the opportunity to assess their non-sterile compounding environment, equipment, and practices to ensure the potential for contamination is minimized.
Compounding Environment
All compounding must be performed in a separate space specifically designated for compounding prescriptions. This space would provide for the orderly placement of equipment and materials to prevent errors and should be designed and arranged to prevent cross-contamination between products. It should be located away from areas of the pharmacy where there is a considerable amount of traffic (e.g., aisles, entrance and exit doors, etc.), to avoid contamination of compounded products with airborne particles, as well as to avoid interrupting or distracting compounding personnel
The following list covers some common and not-so-common areas of possible contamination in a non-sterile compounding environment.
- In the compounding area, it is important to control the temperature and humidity, not only for the comfort of compounding personnel, but also for the stability of the components and compounded preparation. Failure to these factors with a properly designed HVAC system can potentially introduce contaminants into the compounding area.
- Surfaces within the compounding room, from the floor to cabinetry, must be durable and easy to clean. Particular attention should be paid to hard to clean areas such as light fixtures, ceilings, cabinet doors and tops, as well as water supply areas.
- Inadequate cleaning of your compounding area can greatly increase the risks of contamination. Your cleaning process should be clearly outlined in your policies and procedures and include what agents you will use to clean with and what frequency of cleaning is necessary. Developing a cleaning log, that lists all areas in the compounding space/room, can ensure cleaning occurs regularly. Ensure cleaning personnel are adequately trained.
- Water supply areas are a very common source of contamination. Ensure items placed in the sink are cleaned immediately. The sink should also be emptied of all items and cleaned before being used to clean equipment used in non-sterile compounding.
- Keep waste away from compounding areas. Waste removal should occur regularly and be documented in your ongoing cleaning log of activities.
- Avoid storing items on the floor due to higher risks of contamination. Instead, keep products, equipment, ingredients on shelving, or in cabinets.
- Potential sources of contamination could also come from incoming supplies, such as cardboard, or other containers.
- Cleaning personnel are required to know all policies and procedures related to cleaning and decontaminating the equipment, furniture, and facilities, notably those related to hygiene, personal protective equipment, and cleaning and disinfecting tasks.
- When hazardous non-sterile preparations are compounded, cleaning of the premises and equipment must also eliminate chemical contamination from the hazardous products used. Methods used include deactivation, decontamination, and cleaning.
Compounding personnel
Personnel must behave in a professional manner, following all pertinent policies and procedures. For safety reasons, and to avoid possible contamination during non-sterile compounding, personnel must follow the procedures on the Master Formulation Record.
- Clothing can introduce contamination from dust, dirt, or fibres. This can be controlled by using designated compounding gowns or coats that are inspected and cleaned regularly.
- If personnel are wearing jewellery, watches, hats, and/or piercings they should be removed or covered to prevent possible contamination. Even shoes might need to be covered.
- Headphones and earphones can carry contaminants and should be removed before compounding.
- Personal hygiene is a potential source of contamination. Prevent the spread of potential contaminants by trimming or covering nails/beards Avoiding compounding when you are ill, and ensure you are performing good hand hygiene.
- Two lesser known sources of contamination are sunburns and new tattoos
.Ensure any affected skin is fully covered to prevent contamination.
Personal protective equipment (PPE)
- PPE could include chemotherapy gloves, gowns, head/hair coverings, and shoe and sleeve covers. Watch for any sign of tears, punctures, or spilling/staining. Replace these as needed.
- Ensure PPE supplies are stored in areas safe from contamination, such as in a cabinet away from active ingredients or a water supply.
- Ensure PPE, when in use, is kept within the compounding area to avoid spreading contamination and to avoid introducing new contamination back into the compounding area.
- Non-disposable PPE, such as goggles and respirators, can become contaminated after use so it’s important to sanitize with isopropyl alcohol before re-use.
Equipment
- The risk of contamination increases when equipment is cleaned infrequently. To avoid this, clean the compounding equipment immediately after use to prevent cross-contamination.
- Separate the hazardous equipment from non-hazardous equipment, keep them stored in different areas.
Implement contamination mitigation steps when appropriate, and document these in the master formulation record. An example would be measuring and mixing within a sealed device to minimize potential airborne contamination from powder manipulations.